Quality assurance (QA) and quality control (QC) are fundamental to ensuring the success of any construction project. In an industry where errors can lead to costly rework, delays, and client dissatisfaction, maintaining high standards of quality throughout all phases is critical. This article explores key principles for establishing effective QA practices, from defining project expectations to integrating advanced digital tools, while also highlighting the role of QC in verifying that those standards are met.
Data Insights About Quality in Construction
Let’s start with some data points on the quantitative impact that poor or lacking QA and QC can have on the construction process:
- Design errors account for 40-60% of all construction errors.
- According to a study, reworks account for around 5% of the total cost of a construction project and can amount to up to 20% depending on the project.
- Providing and working with sufficient data is becoming increasingly important. A study by Autodesk and FMI highlighted that the use of inaccurate or incomplete data in construction projects contributed to $88.69 billion in rework costs in 2020 alone. This accounted for about 14% of all rework.
- The cost of quality (CoQ), which includes prevention, appraisal, and failure costs, typically represents about 5-6% of the project’s total cost but can rise significantly if issues are not managed effectively during the early phases of the project.
- Rework can impact production, creating as much as a 300% lossin crew productivity.
What is Quality Assurance in Construction?
Quality assurance is a method of avoiding potential mistakes in a construction project by creating ‘rules’ about minimum quality while ensuring all decisions meet these standards. Quality assurance covers things like:
- Materials used: Are they of the right standard, size, shape and material?
- Equipment: Will it work in the environment and is it safe?
- Agreed ways of measuring quality: What does ‘good’ look like?
- Project management: Timeframes, fair bidding processes, agreed budgets, etc.
- Certificates and skills: Do your people have the right skills for the job?
So, quality assurance is about preparation. By building quality into decision-making throughout your projects, you can be confident that you’re ordering the right materials, using the correct equipment and everyone knows what to expect.
Quality Assurance vs. Quality Control
While quality assurance (QA) is about setting standards upfront, quality control (QC) focuses on checking that the finished product meets those standards. QA is a proactive process to prevent defects, whereas QC is reactive, meaning it identifies and corrects defects that have already occurred.
For example, in a construction project, QA involves ensuring the materials, designs, and processes are all aligned to avoid mistakes. QC, on the other hand, involves inspecting the actual work to ensure no mistakes were made. Both QA and QC are essential: QA reduces the need for rework by preventing problems, while QC ensures any issues that do arise are caught and corrected before project completion.
QA is more comprehensive and touches all stages of a project, ensuring standards are in place from planning to material purchasing to execution. QC is more focused on the final product, where teams inspect work for adherence to the set standards. Together, they create a cycle of continuous quality improvement.
5 Golden Rules for Quality in Construction
Achieving quality in construction is a time-consuming and intensive process, which everyone is responsible for. It’s about constantly checking that decisions and work meet the quality assurance standards set.
Here are five golden rules for quality in construction:
1. Set clear definitions of ‘quality’
Everyone working on a project needs to clearly understand what you mean by ‘quality’ and what your expectations are for the project. Document the details and explain them to all subcontractors, suppliers, and project managers. For example, you might decide you want particularly high durability standards for exterior materials, given the project’s location in a region with extreme weather conditions. You’d therefore want subcontractors to be aware of this when making purchasing decisions for materials like roofing, siding, or windows, ensuring they meet both your performance requirements and are suitable for long-term exposure to harsh environmental factors.
2. Detect critical errors early
It is important to note that while QC processes are often well-established and rigorously practiced on most construction sites, the industry tends to focus more on identifying and correcting mistakes rather than preventing them in the first place. QC is excellent at catching issues, but relying solely on QC means that problems are already present, leading to rework and delays.
On the other hand, Quality Assurance (QA) offers the potential to reduce the need for extensive QC efforts by ensuring that defects are prevented during the planning and building phases. By strengthening your QA processes, you can shift the focus from identifying problems after they occur to preventing those issues before they happen. This can lead to fewer delays, lower rework costs, and a smoother handover to the client. The more you invest in QA, the less you’ll need to rely on QC to catch mistakes.
3. Be on top of material purchasing
It’s vital to ensure that all materials and equipment purchased meet your standards. Buying cheaper, lower-quality materials may save money in the short term but could result in problems later. Quality assurance when purchasing materials involves more than just checking if they meet your immediate needs; it also includes verifying that suppliers have strong quality control measures in place and are capable of delivering defect-free products.
The role of QA in the supply chain is crucial to ensure that materials and components are free from defects before they even reach your construction site. Partnering with trusted suppliers who follow robust QA practices ensures that your materials meet both your standards and the project’s quality requirements, thereby improving the overall success of your build.
4. Continuous interaction during the build
All project participants must be able to communicate, discuss issues and verify progress. Quality in construction relies on the site manager constantly monitoring the works, ensuring it meets your pre-agreed definitions of quality.
One of the major issues in construction is rework, which can lead to significant delays and increased costs. Rework occurs when mistakes made during construction need to be corrected before the project can be completed, and it is often caused by unclear communication, plan changes, or poor execution.
By focusing on quality assurance throughout the project lifecycle, you can minimize the risk of rework by ensuring that everyone has the correct and up-to-date information to perform their tasks correctly the first time. This involves clearly communicating plan changes and ensuring that all team members—especially those in the field—understand and adhere to the project standards.
5. Handover and snagging
Once the structure itself is up, quality control (QC) also comes into play at the snagging and handover stage. This stage involves systematic inspections to verify that the as-built structure meets your expected quality standards and adheres to the project’s specifications. QC ensures that all components of the project, from materials to workmanship, comply with the established benchmarks set during the quality assurance (QA) process.
At this point, QC involves conducting thorough inspections, tests, and checks to identify any defects or non-conformities that may have occurred during construction. The snagging process is essential for catching issues such as incorrect installations, material failures, or minor deviations from the design, all of which can impact the functionality or aesthetic quality of the structure. By implementing rigorous QC checks, you can ensure that the project is completed to the highest standards and any identified issues are promptly rectified before the final handover to the client.
How Digitization Helps With Construction Quality Management
At present, much QA and QC in construction relies on manual processes, especially during the building and inspection stages. The site manager conducts frequent inspections of the site, monitoring whether workers are meeting quality assurance standards. But this is a time-consuming and inefficient process, requiring them to use clipboards and write up reports based on their own observations. However, a new generation of construction quality management software aims to make this much more efficient.
A key area where digital workflows make a difference is in the RFI (Request for Information) process. Traditionally, the RFI process is paper-based and slow, with questions and answers passing through several parties before reaching the right people. This often results in delays and miscommunication, which can lead to errors in the build. By digitizing the RFI process, construction teams can ensure that questions and answers are shared instantly across the entire project team, ensuring that the latest information reaches the people who need it in real time.
For example, digital tools like PlanRadar allow RFIs to be raised directly on digital blueprints, ensuring that all team members—both on-site and off-site—can see and respond to the questions. This reduces the risk of miscommunication, as all relevant stakeholders have immediate access to the same information. Additionally, having all RFIs and their responses documented in one place ensures that there is a clear audit trail, which can prevent disputes over quality issues later.
Digital workflows like these not only improve communication but also help to eliminate rework, reduce delays, and ensure that everyone has access to the most up-to-date project information.
PlanRadar construction management software
PlanRadar is a platform designed for documentation, communication, and reporting on construction projects. The software and app support users in processes related to QA and QC. For example, construction defects can be identified on-site and documented directly on digital construction plans or BIM models using text, images, videos, and audio recordings. These tickets are then assigned to the responsible individuals and tracked in real time.
One of PlanRadar’s major advantages is its flexibility: from customizable forms for data collection to generating finished reports, various elements can be tailored to meet your specific content and appearance preferences. In fact, 94% of customers report that PlanRadar helps improve overall quality control, ensuring high-quality project delivery.
The following video demonstrates how a construction manager uses PlanRadar to monitor work quality and oversee all other aspects of the project.
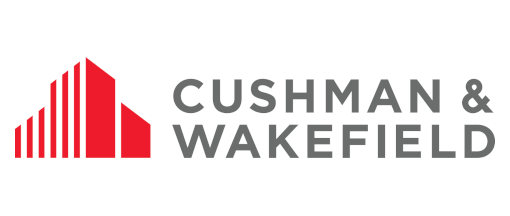
With Planradar, we are able to efficiently measure and document findings on-site and to communicate and process them further.
Interested in seeing how PlanRadar can support your QA and QC? Sign up for a free 30-day trial!