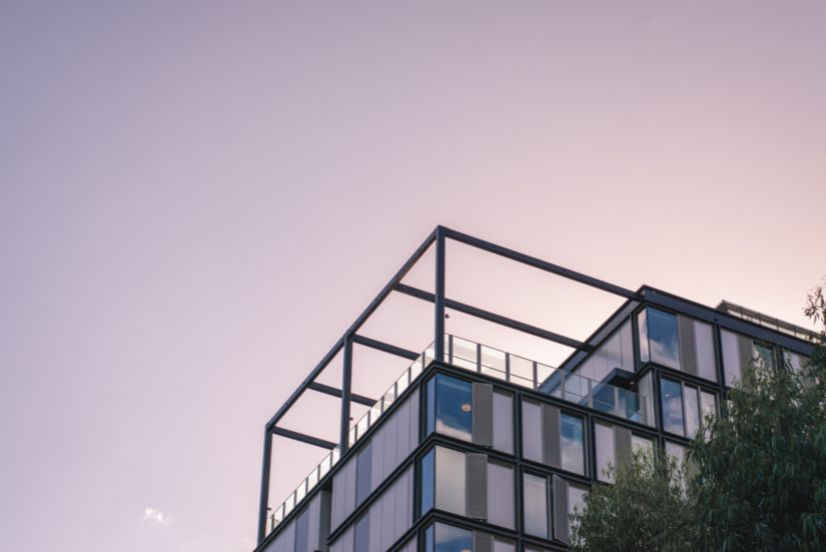
What is construction defect management?
Construcion defect management is the process of identifying, communicating, and fixing defects in a construction project. It helps to reduce construction defects and improve the quality of a project. It’s a critical part of any project manager’s job because it affects many aspects of the project — from budgeting to scheduling to quality assurance. Improving construction defect management capabilities can be just as important as improving overall project management skill set. By learning how to identify problems early on in the process and prevent them from happening again later down the line, construction managers can ensure that their team stays focused on the tasks at hand instead of getting bogged down by unexpected setbacks or delays caused by an inefficient workflow process. Improving defect management is important for construction project managers because it helps them:- Reduce construction defects.
- Improve construction quality.
- Reduce rework and downtime, which saves time and money for the customer, as well as reduces costs associated with litigation.
1. Design an effective defect management system
A defect management system is a tool that helps construction managers to identify, prioritise, and monitor defects in construction projects. It also helps construction managers to solve problems related to the defect management process. The process of defect management is an essential part of any construction project. Defects can cause delays, cost overruns, and even product recalls, which can lead to negative reputational damage. A good defect management system can help minimise these risks by ensuring that the processes are automated and effective. It’s important to know how to set up a defect management system correctly so that it works effectively for a specific project. A good defect management system is:- effective: It should minimise the number of defects and ensure that those that are identified are addressed quickly, efficiently, effectively, and economically
- scalable and adaptable: It should be able to handle changes in the size or complexity of the project, and it should accommodate new tools as they emerge.
- sustainable: It should promote continuous improvement and learning so that it can evolve as needs change.
- responsive to stakeholder needs: It should ensure that all stakeholders have a voice in the process, their concerns are addressed, and they feel like their interests are being served.
- flexible: It should provide for reasonable changes in scope or schedule without disrupting the process. It should allow for different approaches to managing defects depending on the type of project and its circumstances.
- comprehensive: It should cover all types of defects, including those that are discovered during development, testing, and post-release support.
- transparent: It should provide clear accountability for managing defects and adequate documentation to help others understand the process.
- efficient: It should minimise overhead and reduce the time and effort required to manage defects.
- cost-effective: It should provide value for money by delivering high-quality outcomes while minimising the cost of fixing bugs or rework that might otherwise have been necessary.
2. Implement defect management software to manage defects
The most effective strategy is to use a defect management software solution. This can be used to manage defects, track progress and improve project quality. A defect management software platform will allow a construction manager to create a custom workflow. They can also use these tools on any device so that they don’t have to worry about getting everyone in the office on the same page when it comes time for reporting back or other tasks related to construction defects management. Defect management tools can be used to manage defects in construction projects, reduce costs, and improve project quality. They are also customizable so that construction managers can create custom workflows that are specific to their needs. Another advantage of using construction defect management software is that employees and subcontractors can use these tools on any device. With a digital collaboration tool, construction managers don’t have to worry about getting everyone in the office on the same page when it comes time for reporting back or other tasks related to construction defects management.3. Use 3D and BIM to map, plan and understand the construction project sequence in advance
Building Information Modeling (BIM) is a tool that allows construction managers and designers to create a 3D model of a construction project. This can help construction quality assurance managers understand the construction sequence in advance and identify and fix defects before they happen, saving time, money, and resources. The first step in using BIM for defect management is to get the team familiar with it. A simple tutorial will teach them how to use their computer or tablet so they can start creating models right away. Once this has been accomplished, there are many different types of projects that could be created:- Levelling plans (where every surface level is up or down)
- Roofing drawings (where every roof line shows exactly where each piece of roofing material should be placed)
- Surface models (where all surfaces are shown in great detail)
- Exterior and interior views (where all walls, doors, and windows are shown in detail)
- Structural drawings (where all load-bearing structures are shown in great detail)
- Electrical layouts (where every wire is shown in its correct position)