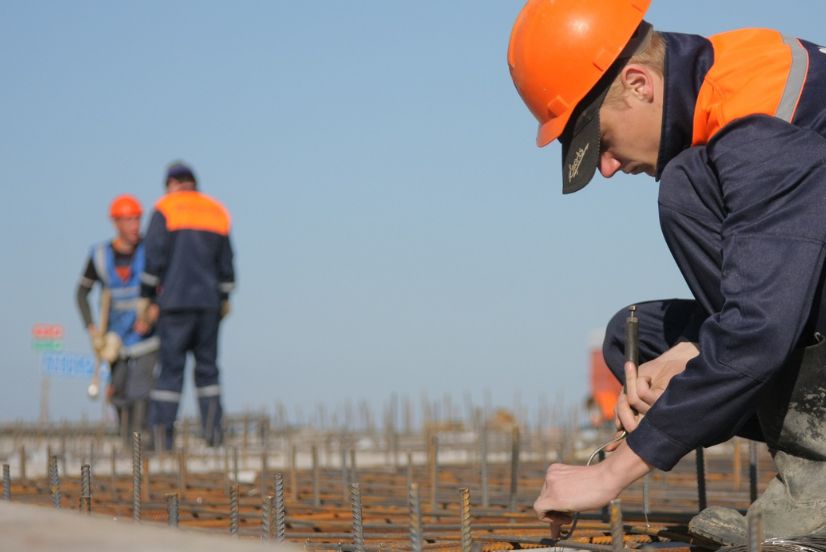
What is construction defect management?
Defect management is a process that helps to monitor and manage construction defects. Defects can be the result of errors in drawings, building plans or specifications, inadequate site supervision, poor workmanship, or other unforeseen circumstances. Some examples of common construction defects include:- Water infiltration: This can include issues with leaks in the roof, walls, or foundation of a building, which can lead to damage to the structure, mould growth, and other problems.
- Structural issues: Defects in the design or construction of the building’s structure can lead to issues with stability, safety, and load-bearing capacity.
- Electrical and plumbing defects: These can include issues with wiring, electrical panels, and plumbing systems, which can lead to problems with power, lighting, and water supply.
- HVAC defects: Defects in the heating, ventilation and air conditioning systems can lead to issues with temperature control, indoor air quality, and energy efficiency.
- Finish defects: These can include issues with paint, wallpaper, flooring, and other finishes, which can affect the appearance and durability of a building.
Why is construction defect management important in construction projects?
Construction defect management is critical for any project, but why?- It helps to reduce costs. The ability to identify defects and resolve them early will help with cost savings. This can happen in several ways, including avoiding unnecessary inspections or paying for repairs after the fact.
- It improves quality. Poor quality products can negatively impact the bottom line when it comes time for replacement or repair because they may not last as long as expected. This can also lead to spending more resources down the line when things break down sooner than expected.
- It saves time. Construction managers can save time by identifying and resolving defects early in the process, which means the project will be finished faster than expected.
Changes in the industry impacting defect management
Over the last two decades, construction projects have become more complex, more expensive, and even more difficult to learn from because of changing business conditions and new technologies that continually disrupt our industry. Construction projects have become increasingly complex over time for several reasons, including:- Advancements in technology: New materials, systems, and techniques are constantly being developed and implemented in construction projects, which can make them more complex to design, build, and manage.
- Increased regulations and compliance requirements: Construction projects are subject to a wide range of regulations and compliance requirements, including building codes, environmental laws, and safety regulations. This can add complexity to the construction process and require more documentation and oversight.
- Greater demand for sustainability and energy efficiency: There is an increasing demand for sustainable and energy-efficient buildings, which can require the use of specialised materials and systems, as well as more complex design and construction processes.
- Complex project requirements: Construction projects are becoming more and more complex with the increasing demand for multi-functionality, like smart buildings, and integration of new technologies like IoT, automation, and AI.
Stakeholders in construction defect management
A stakeholder can be anyone who has an invested interest in a construction project—this could be an architect or engineer, a contractor or subcontractor, a property owner or tenant, etc. They all have different perspectives on how things should work out at each stage of development and what needs to happen next depending on their role within the project.- The owner is the person or entity who pays for a construction project and gains title to the property upon completion, which could be the landlord.
- The contractor is responsible for managing all of the subcontractors, organising their schedules, and keeping everyone on task. They also provide labour, resources, and materials necessary to complete the job by specifications outlined in a contract between them and the owner.
- The construction manager is a vital link between the client and the contractor, with responsibility for ensuring that all parties are working together to achieve their goals. Their role is to coordinate all aspects of a project, from managing resources to managing risk.
- The construction defect manager has the responsibility for managing the defects that arise during the construction process. They are responsible for investigating complaints from third parties and conducting due diligence investigations into possible defects in order for them to be resolved before they become more serious issues.
- The engineer is the one who ensures that a building is structurally sound, that it meets all safety standards and regulations, and that it will be able to stand up to the elements while providing its intended function.
- The architect is a licensed professional who designs buildings by drawing up plans using CAD (computer-aided design) software programs. Architects may also provide advice about engineering issues related to structural integrity, as well as environmental concerns such as energy efficiency or indoor air quality.
How does the construction defect management process work?
Defect management is a process that can be used to identify and address construction defects, including deficiencies in design and the installation of building materials. The steps involved in the construction defect management process can vary depending on the specific project and the nature of the defects, but typically include the following:- Identification: The first step is to identify and document any defects that have occurred during or after construction. This can be done through visual inspections, testing, and other methods.
- Analysis: Once the defects have been identified, the next step is to analyse the cause and extent of the problem. This can involve reviewing design and construction documents, interviewing contractors and other stakeholders, and conducting further testing or inspections.
- Remediation: After the cause and extent of the defects have been determined, the next step is to develop and implement a plan to repair or remedy the problem. This can involve making repairs, replacing materials or systems, or taking other corrective actions.
- Monitoring: The next step is to monitor the progress of the repairs and ensure that the defects have been properly addressed. This can involve conducting follow-up inspections, testing, and other methods to confirm that the repairs have been successful.
- Closeout: The last step is to close out the project – this can include documenting the defects and the actions taken to address them, submitting final reports, and completing any other necessary administrative tasks.
Critical tools for construction defect management
The following are important tools and processes that are used in construction defect management:- A construction defect list – A construction defect list is a comprehensive record of all defects on site, including their severity, location, and stage they are at. It is important to maintain this list so that it can be used to track progress and make sure nothing slips through the cracks. It’s usually organised by type or location, and there are usually several versions of the list: one for each party involved in the project. These lists help ensure that everyone is aware of any issues on site and can work together to resolve them quickly.
- Construction defect management scheduling: The scheduling process outlines each step in the defect management and rework project, along with its duration (how long it takes), who does what part(s), when they do them (in order), and what documentation is required after each task has been completed successfully or unsuccessfully.
- Construction defect management software: The software helps manage projects by tracking defects, their owners, data gathered, and solutions proposed. It can be used to create reports that show how the project is progressing and the status of the defects. Since it is digital, it allows for online collaboration and has one source of truth when it comes to all the defects related to the construction project.
Steps to ensuring a high-quality construction project
While it might be impossible to make sure that there are no or extremely few defects in any project, constructions projects can follow a few steps to manage the defect process better:- All stakeholders must agree on what constitutes a defect before work begins so they can properly report them later on. If there’s disagreement over what constitutes a defect or how to deal with it, delays could occur as discussions are held among different parties about what needs to be done.
- The design team must consider the building’s intended use and the materials used in construction when creating a plan. This will help avoid structural defects. For example, if you want to build an office building, you might need to make sure that there are no columns directly under windows so that people don’t trip over them.
- The construction crew should follow the plans and specifications precisely. This will help ensure that all materials used in construction meet their required specifications.
The role of technology in construction defect management
The main function of technology in construction defect management is to help manage the process of construction defect management. While this may seem fairly straightforward at first glance, there are many ways that technology can help to:- Improve quality by providing real-time data about issues between stakeholders throughout the process
- Increase efficiency by allowing for better collaboration between stakeholders throughout the process
- Improve effectiveness by allowing for a more accurate analysis of past issues
- Allow for easier communication between stakeholders by providing a platform for them to communicate with each other and share information
- Provide greater control over the process by allowing for better visibility into what is happening at any given time.
- Technology and construction management software can play an important role in the construction defect management process by helping to streamline and automate various tasks, such as:
- Document management: Construction management software can help to store, organise, and share important documents and information related to the project, such as design and construction documents, inspection reports, and other data. This can make it easier to access and analyse relevant information when identifying and analysing defects.
- Defect tracking: Some software allows to track and manage defects throughout the construction process, from identification to remediation. This can include features such as creating and assigning tasks, setting priorities, and tracking progress and completion.
- Communication and collaboration: Construction management software can also help to improve communication and collaboration among project stakeholders, such as architects, engineers, contractors, and owners. This can include tools such as messaging, file sharing, and online meetings, which can help to ensure that everyone is on the same page and that issues are addressed in a timely manner.
- Reporting and data analytics: Construction management software can also provide reporting and data analytics capabilities that can help to identify trends, patterns, and areas for improvement in the construction process. This can include tools such as dashboards, charts, and graphs that can help to quickly and easily visualise important data and make data-driven decisions.