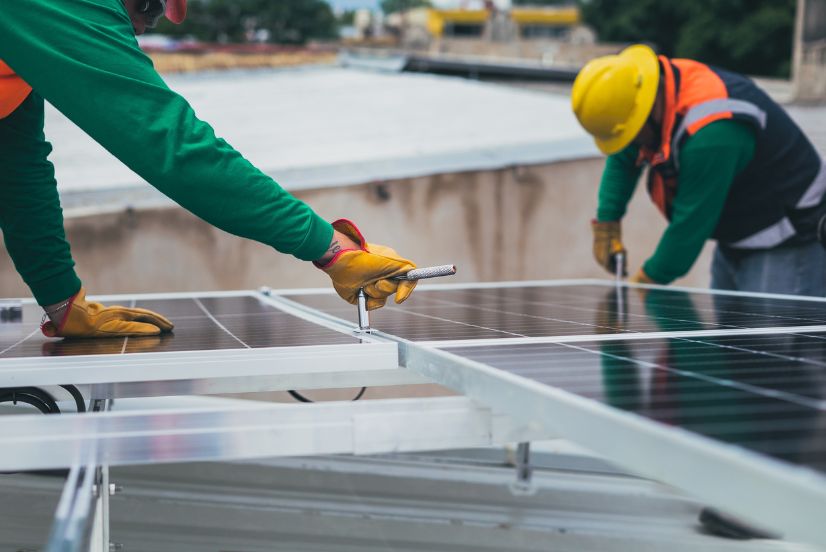
Challenges and pitfalls in construction defect resolution
While collaborative defect management is a highly recommended approach, it does come with its share of challenges. One common obstacle is the complexity of construction projects themselves. The multifaceted nature of construction can lead to miscommunication and a lack of clarity, especially when multiple teams, subcontractors, and stakeholders are involved. This complexity can make it challenging to pinpoint the exact root causes of defects and to ensure that all relevant parties are on the same page regarding defect resolution. Additionally, time constraints can add to the difficulty. Construction projects often operate on tight schedules, and any delays in defect resolution can have a cascading effect on project timelines and budgets. Moreover, conflicting interests among stakeholders can create hurdles. Different parties may have varying priorities, making it essential to find common ground and alignment on defect management strategies. Furthermore, navigating legal aspects and contractual obligations can pose challenges, particularly when disputes arise. These complexities demand well-thought-out strategies to overcome the pitfalls and ensure that collaborative defect management remains effective throughout the construction process.The benefits of collaborative defect management
Collaborative defect management in construction offers a wide range of advantages that can transform the dynamics of any construction project. Improved efficiency and cost savings are among the most tangible benefits. When construction teams work together to identify and resolve defects promptly, it minimizes the chances of defects escalating into more significant issues that demand extensive time and resources for resolution. This proactive approach reduces project delays, potentially hefty rework costs, and disruptions to the construction timeline. Consequently, it translates into substantial savings and ensures that projects stay on budget and on schedule. Enhanced quality control is another vital outcome of collaborative defect management. By involving various stakeholders, each with their area of expertise, it becomes easier to maintain and enforce stringent quality standards. These standards cover everything from materials and workmanship to compliance with safety regulations. A collaborative approach allows for real-time monitoring and the swift rectification of any deviations from these standards, ensuring that the final construction product is of the highest quality. Moreover, it fosters a culture of continuous improvement, where lessons learned from defect management are applied to subsequent projects, raising the overall quality of construction efforts. Lastly, reputation management and client satisfaction are paramount in the construction industry. A project marked by effective defect management not only impresses clients but also establishes a positive reputation for the construction team. Satisfied clients are more likely to return for future projects and provide positive referrals, creating a virtuous cycle of success for construction firms. In the competitive world of construction, these benefits underscore the transformative power of teamwork and collaboration in defect management.Effective communication in defect management
Clear and effective communication is a crucial aspect of successful defect management in construction. To ensure seamless collaboration among various project stakeholders, it’s essential to establish clear communication channels. This includes defining reporting hierarchies, setting up regular project meetings, and designating responsible parties for defect resolution. Such channels provide a structured framework for sharing information and ensuring that everyone is informed about ongoing defect management efforts. The importance of timely reporting cannot be overstated. In construction, defects can emerge at any phase of the project, and swift reporting is crucial to address them promptly. Delayed reporting can lead to the exacerbation of defects, causing project delays and additional costs. Therefore, it’s imperative that project teams prioritize the immediate reporting of any defects, regardless of their perceived significance. In today’s digital age, collaboration tools and technologies have revolutionized defect management. Software solutions, cloud-based platforms, and mobile applications enable real-time reporting and data sharing, streamlining the defect resolution process. These technologies facilitate faster decision-making, data analysis, and communication among team members, ultimately enhancing the efficiency and effectiveness of defect management efforts.Best practices for building collaborative teams
1. Multidisciplinary teams
In construction defect management, the power of teamwork shines through when multidisciplinary teams collaborate seamlessly. These teams comprise professionals with various areas of expertise, including architects, engineers, project managers, contractors, and quality assurance specialists. Each member brings a unique perspective to the table, allowing for comprehensive defect identification and resolution. For instance, an architect might spot design-related defects, while an engineer could identify structural issues. This multidisciplinary approach ensures that no defect goes unnoticed and that each one is addressed with precision. Key takeaways:- Multidisciplinary teams leverage diverse expertise.
- They enhance defect identification and resolution.
- Collaboration among professionals from different fields is essential for comprehensive defect management.
2. Roles and responsibilities
Effectively defining roles and responsibilities within a defect management team is paramount. Clear delineation ensures that each team member understands their tasks and areas of accountability. For example, a project manager might oversee defect tracking and reporting, while a quality control specialist focuses on defect verification and rectification. Such clarity minimizes confusion, prevents overlaps, and fosters a sense of ownership among team members, driving efficient defect management. Key takeaways:- Clear roles and responsibilities prevent confusion.
- They lead to efficient defect management.
- Accountability among team members is essential for success.
3. Conflict resolution strategies
In the collaborative landscape of construction defect management, conflicts may arise. Effective conflict resolution strategies are vital to maintain teamwork and productivity. For example, when disagreements surface between team members on defect prioritization, a conflict resolution process can help find common ground. This might involve open communication, mediation, or seeking input from an unbiased third party. By addressing conflicts swiftly and constructively, construction teams can prevent disruptions and maintain their focus on defect resolution. Key takeaways:- Conflicts are common in collaborative environments.
- Effective resolution strategies prevent disruptions.
- Open communication and mediation are essential conflict resolution tools.
4. Training and development
Construction defect management teams must continually invest in training and development. Hypothetically, consider a scenario where a team undergoes regular training sessions on emerging construction technologies and defect identification techniques. This ongoing learning empowers team members with up-to-date knowledge and skills, making them better equipped to handle evolving challenges. Training and development are not one-time events but rather continuous processes that ensure teams remain at the forefront of defect management practices. Key takeaways:- Continuous training keeps teams updated.
- It enhances skills and knowledge.
- Ongoing learning is essential in the ever-evolving construction landscape.
5. Continuous improvement
In the hypothetical context of construction defect management, continuous improvement is a driving force. Imagine a scenario where teams regularly conduct post-project evaluations, analysing their defect management performance. This evaluation process identifies areas for enhancement, leading to the implementation of improved defect resolution strategies. Continuous improvement ensures that each project benefits from the lessons learned in previous ones, elevating overall defect management efficiency. Key takeaways:- Post-project evaluations identify areas for improvement.
- Implementing enhancements leads to more efficient defect management.
- Lessons learned benefit future projects, fostering continuous improvement.