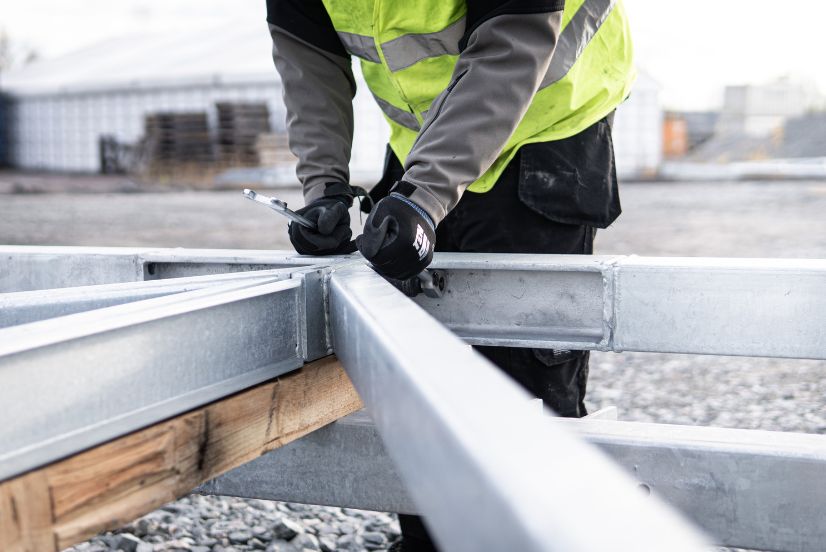
Dealing with a range of building defects on any construction project can be challenging, time-consuming, and costly, especially if litigation is involved. However, there are proven, proactive steps that you can use through various project stages to reduce building defects and the risk of liability.
There are many reasons why construction projects go wrong. A range of factors can contribute to building defects, including poor planning, inadequate training, and inadequate quality control. Regardless of whether a defect is major or minor in nature, a problem remains: defects typically aren’t discovered until long after completion of the work, and defending against defect claims can be a time-consuming (and expensive) task.
To reduce the chance of construction defects and the costly claims that can accompany them, quality assurance is an absolute must-have in all aspects of construction project design, build and operation.
What exactly is a construction defect?
Construction defects typically relate to a weakness in the building process, such as in the design, materials, or craftsmanship, which results in a failure in some component of the structure being produced and harms a person or part of the building (financial or otherwise). To put it another way, there must be all three of the following for there to be a construction defect:
- a flaw in the actual construction process (due to subpar design, materials, or workmanship);
- the flaw must result in a failure in the structure (which is being built during the project);
- and the failure must cause harm to a person or piece of property (whether in the form of monetary losses or other types of damages).
A flaw could occasionally be as straightforward as not measuring up to a client’s expectations. Other times, it may be as serious as a fault in the building’s structure. Of course, depending on the origin and seriousness of the problem at hand, construction flaws and the consequences that follow will vary substantially.
What kinds of construction defects are the most common?
Construction defects are often categorised as either patent or latent after identifying the type of defect. A patent defect is one that is well known or immediately noticeable upon inspection. They are the issues a contractor, sub, or member of another profession should want to discover during routine inspections. On the other side, latent defects are those that are hidden or otherwise difficult to spot. Even someone who properly inspects the work may be unlikely to find latent defects.
When a patent defect is clear, it usually signifies that a simple repair is possible. Since these defects are mostly cosmetic in nature and just on the surface, they are often easy to access and fix. On the other hand, since latent defects aren’t readily apparent, it typically means they’re hidden or even a faulty system deep within a project. Latent defects consequently tend to be a little more challenging.
Let’s examine the main three categories of building defects in greater detail:
1. Design defects
These defects are the result of inaccurate and disorganised construction paperwork produced by a design professional. Design defects are errors or omissions in the work. Defects typically necessitate redesigning the project and replacing a component item, whereas omissions can be fixed by expanding the scope of work for the contractor through change orders.
2. Materials defects
“Material defects” are defects caused by faulty or damaged construction materials. When these faults originate with the manufacturer, the parties utilising the materials frequently don’t learn about them until after they’ve been integrated into the project. Due to the potential need for additional work and new materials, material defects are often particularly expensive and time-intensive to repair.
3. Craftsmanship defects
Workmanship defects are frequently the first idea that comes to mind when people think about construction defects. When a contractor doesn’t create a structure or component part in line with the construction documents, these defects arise. Workmanship defects can range from straightforward cosmetic faults to issues with structural integrity. It can be very difficult to assign responsibility and figure out how the project’s quality assurance and building standard of care was breached.
How can I reduce defects in my business’s construction projects?
According to a recent NSW Government report, the average cost to resolve building defects was around $331,829. In addition to increasing repair costs, sub-par work may put your business’s reputation on the line and cost you future project opportunities. There are several ways to reduce the risk of defects in your construction projects. Some are simple to implement and cost little or nothing; others require more resources but may help you avoid costly litigation.
To minimise defects and associated claims, follow the tips below to ensure that your construction work is defect-free:
- Make sure all stakeholders have access to the latest construction drawings, blueprints and project plans at all stages of construction
- Comply with manufacturer’s recommendations and all available industry compliance guidelines
- Choose quality materials for your project that meet National Construction Code (NCC) guidelines
- Conduct subcontractor performance evaluations as required
- Perform routine site quality control inspections to ensure all project activity is up to standard
- Build a culture of clear jobsite communication and open collaboration with your team
- Document all decisions, changes, requests, communications and tasks on-site and off-site, no matter minor or major
Proactively addressing these potential issues throughout the project lifecycle can help you reduce incidences of defects and errors at any stage of construction, helping you mitigate the risk of litigation. Here are some of the key project items to keep in mind, that you can take on-site or during the build phase to reduce the possibility of building defects and potential liability claims:
- Conduct a thorough pre-construction meeting with your client to discuss the project scope and expectations for quality control
- Use clear contracts to define what is expected from both parties during construction, including timelines and quality control procedures
- Maintain a close working relationship with your team members throughout all stages of the project, including inspections and reviews
- Build in regular communication between your team members and clients so that everyone is aware of any changes or challenges that arise
- Keep detailed time-stamped and transparent task trails of any defects, changes or adjustments throughout the build
These practical tips can help you save thousands of dollars on rectifying the issues and minimise the time and effort spent on damage control.
With thousands of records to manage, cloud-based platforms and apps for defect management can prove to be an invaluable tool to simplify and control this complex and time-consuming process. Want to take the stress out of defect management? Use PlanRadar as your go-to project management platform for construction projects – book a demo or get in touch today!