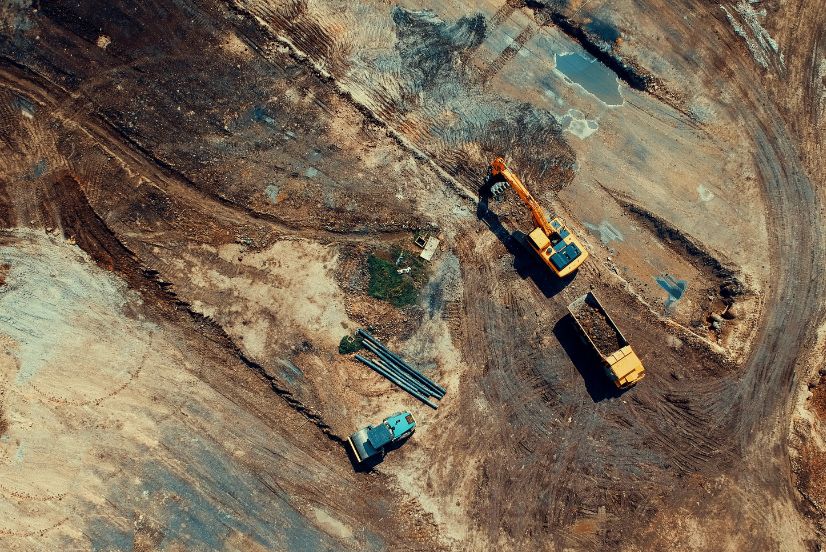
The world has experienced unprecedented change stemming from COVID-19, with energy and resources sectors such as mining, oil and gas and metals among the most heavily affected. Customers now hold more market power as a result of a significant decline in demand, escalating competition. For the energy and resources industries, this, coupled with supply-chain instability, has resulted in a severe margin squeeze.
In addition to finding ways to boost their short-term performance and gain a competitive edge in markets that are contracting, many mining businesses are also looking for ways to assure their long-term sustainability in the new normal through healthy transition.
Many mining management companies are required to maintain a minimum of certain highly experienced operations and maintenance personnel on-site, but some industries, like software development, have been able to transition to remote work without any difficulty. However, research is showing that organisations who embrace new structures or systems to support remote working could help to future-proof their businesses against market volatality.
In this article, we examine some of the challenges that mining companies can face, offer best practises for enhancing remote working, and discuss the components of a successful long-term transformation.
The key challenges of remote working in mining
Companies in the mining industry that switch to remote working can face immediate communication issues, many of which are exacerbated by legacy technological infrastructure and decreased organizational productivity. On the other hand, as many remote mining sites also have certain constraints (such as limited internet connection), mining companies relying solely on the current digital tools is often an inadequate answer.
In addition, working remotely itself has its own set of difficulties over the COVID-19 pandemic. Research demonstrates that remote employees may believe they lack the expertise needed to thrive away from typical site operations for an extended period of time, even during normal circumstances. Because of this, it’s possible that businesses’ earlier efforts to safeguard employees’ well-being and maintain operational effectiveness are proving insufficient now.
How can teams align on remote working for mining operations?
Any mining business must pause and consider how to maintain these dynamic work practises established during the COVID-19 pandemic sustainably in the long term. The fundamental nature of most workplaces has changed significantly – as a result, a number of more recently developed processes, adopted digital tools, and new team structures may prove to be long-term fixes that make mining businesses more resilient, effective, and secure.
Companies today must provide remote working capabilities and mining management software access to mission-critical personnel, and match expectations throughout the entire organisation; covering even the most fundamental factors like coordinating across time zones and working hours.
The following six recommended practises can assist in reestablishing remote working arrangements to guarantee mining teams continue to thrive and function effectively in a changing landscape:
1. Learn to lead remotely, rather than micromanage
Setting the direction of the work, making connections, and inspiring your mine site workforce all depend on leadership. Businesses can also benefit by delegating decision-making authority – allowing teams to act independently of one another’s locations in order to minimise any unneeded delays.
2. Promote a safety-conscious and inclusive work culture
The top concern for mining industries is always the safety of the workforce, as well as their ongoing health and wellbeing. Some teams may find it challenging to find themselves unexpectedly working from home, possibly for the first time. As a result, mining site stakeholders should lay out precise instructions for how to respond in these novel situations. This can be managed by actively looking for chances to catch up on a personal basis, or by conducting surveys every two weeks to get feedback on teams’ thoughts and concerns.
3. Create a team structure that focuses on results and has distinct functions
Any new approach to a job necessitates changing the range of a team’s responsibilities, as well as their position within projects; a leader’s responsibility should be to coordinate a team’s efforts. Redefining the scope of ongoing mining site projects is necessary, and priority should take into account the time allotted to each activity. For instance, remote mining process engineers can also be reassigned as subject matter experts, spending their time mentoring junior team members on site or remotely, codifying their site knowledge internally, and leading problem-solving sessions—tasks that might not normally be of the utmost importance on a day-to-day mining site.
4. Focus on frequent, high-quality team interactions
This is especially important for on-site mining operations, since discussions frequently take place ad hoc and there isn’t always direct monitoring or a set schedule. To make sure mining teams are motivated and on task, team leads should arrange meetings on a frequent basis, whether they be daily or weekly. To keep mining project management operating smoothly, clear decision-making and escalation pathways are crucial. Regardless of where each team member is physically located, regular touchpoints with the entire team are essential for maintaining coordination, preventing misunderstandings, and maintaining a progress-oriented mindset for your team.
5. Create a widely accessible, single source of truth
The primary objective for effective remote working for any mining management company is to improve communication among all parties. Any mining operations that depend on regular communication and comments from on-site process engineers or directors can benefit most from open transparency. Better planning and streamlined project outcomes can be achieved by filling in knowledge gaps from one shift to the next, outlining current tasks, informing site teams of impending deadlines or items that need to be implemented, and closely tracking deployment.
6. Adopt a comprehensive set of digital tools for remote mining work, quick assessments, observation, and analytics
Beyond technology like digital twins or virtual reality (VR) modules used for remote training sessions, countless creative solutions and tools can be employed to improve daily mine site operations, enabling remote help at every stage of any project. For instance, cameras can be installed on essential excavators to find meaningful potential for improvement, overall equipment effectiveness and enable daily performance management for the site manager. Drones can be used to conduct geological surveying after detonation and blasting. Experts can also use smart glasses to perform remote walkthroughs in real-time video assessments in collaboration with on-site staff.
In addition, mining businesses should always make sure that the necessary procedures and frameworks are in place to support secure remote working. When using digital collaboration platforms or mining management software, especially for workers who are not accustomed to working outside of company premises, it is important to always be mindful of cybersecurity best practices.
Taking learnings into a hybrid work site
There is no one-size-fits-all approach to hybrid work since mining, energy and resources industries can significantly differ from one another. Mining business stakeholders must consequently rethink the “how we work” strategy of their organisation in terms of its structure, people, processes, and technology:
- Structure: The post-COVID hybrid work shift may be useful in identifying projects or services that may be permanently moved to remote models, as well as those that could be discontinued, adapted or restructured.
- People: The transition from on-site to hybrid working may necessitate a significant investment in mining workforce engagement and skill training, much of which can be provided via digital platforms.
- Processes: Organizations should investigate which current site procedures have successfully increased operational transparency, decreased the likelihood of errors or site shutdowns, and increased productivity.
- Technology: Leaders should help accelerate tech modernisation and project management software for better access to information, and help reduce on-site risks.
Finally, mining businesses need to consider the sequence in which these improvements should be put into practise. Which adaptation—to people, processes, infrastructure, or technology—is most crucial? Once this has been established, the portfolio currently available for infrastructure improvement may be evaluated, and a timeline for the transition can be established.
However, success hinges on company leaders’ capacity to adopt a mentality shift throughout their organisations – one that supports the next normal and future-proofs the business against periods of further volatility. By doing this, you can make sure that both essential and non-essential mining teams may arrive at work as safely as possible, that top talent and experience can be drawn and used remotely, and that ever-more-efficient or high-urgency operations require less time on-site when COVID-19 restrictions are in place.
With the right tools, mining companies can be more efficient in managing their workforce safety requirements, identifying and mitigating potential risks, and creating detailed plans that will help them prepare for shifts in the work or COVID-19 regulatory landscape. If you’re looking to get started with safety and operational planning for your mining sites, or would like to get started on your journey with mining management software, you can start your 30-day free PlanRadar trial here.